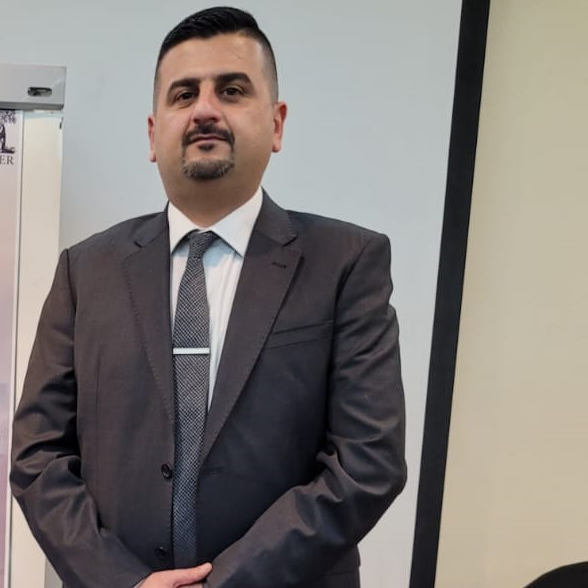
Izzat Al-Darraji received the Ph.D. degree (2018) in Mechanical Engineering from Gaziantep University in Mechatronics applications research, Turkey, MSc degree (2010) in Mechatronics Engineering from Siegen University, Germany, and the BSc degree (2003) in Mechatronics Engineering from University of Baghdad, Iraq. He is an assistant professor with twenty years of experience working in university of Baghdad. He does research in drones, mechatronics, and robotics. He is responsible for teaching mechatronics applications, network system automation, PLC, control and measurement, project management, and microprocessor subjects.
- Strong communication skills and self-motivated person.
- Ability to challenge problems and finding solutions.
- Modelling, control, and design of drone
- Modelling, control, and design of aerial manipulator
- Kinematic analysis of robots.
- Dynamics analysis and control of robots.
- Digital twins of systems
- Design and control grasping manipulators.
- Modelling and simulation of dynamic systems.
- Building virtual reality of systems.
- Programming and wiring PLC: siemens, DELTA, G6 series
- Programming and wiring HMI: siemens, DELTA
- Reverse Engineering using 3D scanner and 3D printer.
- Programming microcontroller.
- Programming and simulation industrial robots by MATLAB
- Design of CNC machines
- Programming AutoCAD dxf files and G-Code files for CNC machines.
- Drawing and manufacturing using solidworks and 3D printer.
- Design electronic interface circuits with supervisory control and data acquisition.
- Programming microprocessor using Assembly language.
- Programming touchscreen using Mitse 3.
- Teaching B.Sc and M.Sc courses at Automated Manufacturing Department/ Alkwarizmi College of Engineering/ University of Baghdad.
- Supervising Labs of: mechatronics applications, PLC, network system automation at Automated Manufacturing Department/ Alkwarizmi College of Engineering/ University of Baghdad.
- Supervising B.Sc and M.Sc students projects at Automated Manufacturing Department/ Alkwarizmi College of Engineering/ University of Baghdad.
- Member of the Engineering consulting office/ Alkwarizmi College of Engineering/ University of Baghdad.
- Member of the German Alumni Akademy/ University of Siegen.
- Mechatronics
- Drones
- Robotics
- PLC
Mechatronics applications
- Industrial robots and automation/ M.Sc degree
- mechatronics applications/ B.Sc degree
- network system automation/ B.Sc degree
- PLC/ B.Sc degree
Supervising many projects of students.
A Wearable Robotic Knee (WRK) is a mobile device designed to assist disabled individuals in moving freely in undefined environments without external support. An advanced controller is required to track the output trajectory of a WRK device in order to resolve uncertainties that are caused by modeling errors and external disturbances. During the performance of a task, disturbances are caused by changes in the external load and dynamic work conditions, such as by holding weights while performing the task. The aim of this study is to address these issues and enhance the performance of the output trajectory tracking goal using an adaptive robust controller based on the Radial Basis Function (RBF) Neural Network (NN) system and Hamilton
... Show MoreThe process of controlling a Flexible Joint Robot Manipulator (FJRM) requires additional sensors for measuring the state variables of flexible joints. Therefore, taking the elasticity into account adds a lot of complexity as all the additional sensors must be taken into account during the control process. This paper proposes a nonlinear observer that controls FJRM, without requiring equipment sensors for measuring the states. The nonlinear state equations are derived in detail for the FJRM where nonlinearity, of order three, is considered. The Takagi–Sugeno Fuzzy Model (T-SFM) technique is applied to linearize the FJRM system. The Luenberger observer is designed to estimate the unmeasured states using error correction. The develop
... Show MoreElectronic remote identification (ER-ID) is a new radio frequency (RF) technology that is initiated by the Federal Aviation Authorities (FAA). For security reasons, traffic control, and so on, ER-ID has been applied for drones by the FAA to enable them to transmit their unique identification and location so that unauthorized drones can be identified. The current limitation of the existing ER-ID algorithms is that the application is limited to the Wi-Fi and Bluetooth wireless controllers, which results in a maximum range of 10–20 m for Bluetooth and 50–100 m for Wi-Fi. In this study, a mathematical computing technique based on finite state automaton (FSA) is introduced to expand the range of the ER-ID RF system and reduce the ene
... Show MoreAerial manipulation of objects has a number of advantages as it is not limited by the morphology of the terrain. One of the main problems of the aerial payload process is the lack of real-time prediction of the interaction between the gripper of the aerial robot and the payload. This paper introduces a digital twin (DT) approach based on impedance control of the aerial payload transmission process. The impedance control technique is implemented to develop the target impedance based on emerging the mass of the payload and the model of the gripper fingers. Tracking the position of the interactional point between the fingers of gripper and payload, inside the impedance control, is achieved using model predictive control (MPD) approach.
... Show MoreEvery so often, a confluence of novel technologies emerges that radically transforms every aspect of the industry, the global economy, and finally, the way we live. These sharp leaps of human ingenuity are known as industrial revolutions, and we are currently in the midst of the fourth such revolution, coined Industry 4.0 by the World Economic Forum. Building on their guideline set of technologies that encompass Industry 4.0, we present a full set of pillar technologies on which Industry 4.0 project portfolio management rests as well as the foundation technologies that support these pillars. A complete model of an Industry 4.0 factory which relies on these pillar technologies is presented. The full set of pillars encompasses cyberph
... Show MoreAbstract. This work presents a detailed design of a three-jointed tendon-driven robot finger with a cam/pulleys transmission and joint Variable Stiffness Actuator (VSA). The finger motion configuration is obtained by deriving the cam/pulleys transmission profile as a mathematical solution that is then implemented to achieve contact force isotropy on the phalanges. A VSA is proposed, in which three VSAs are designed to act as a muscle in joint space to provide firm grasping. As a mechatronic approach, a suitable type and number of force sensors and actuators are designed to sense the touch, actuate the finger, and tune the VSAs. The torque of the VSAs is controlled utilizing a designed Multi Input Multi Output (MIMO) fuzzy controll
... Show MoreAerial Robot Arms (ARAs) enable aerial drones to interact and influence objects in various environments. Traditional ARA controllers need the availability of a high-precision model to avoid high control chattering. Furthermore, in practical applications of aerial object manipulation, the payloads that ARAs can handle vary, depending on the nature of the task. The high uncertainties due to modeling errors and an unknown payload are inversely proportional to the stability of ARAs. To address the issue of stability, a new adaptive robust controller, based on the Radial Basis Function (RBF) neural network, is proposed. A three-tier approach is also followed. Firstly, a detailed new model for the ARA is derived using the Lagrange–d’A
... Show More