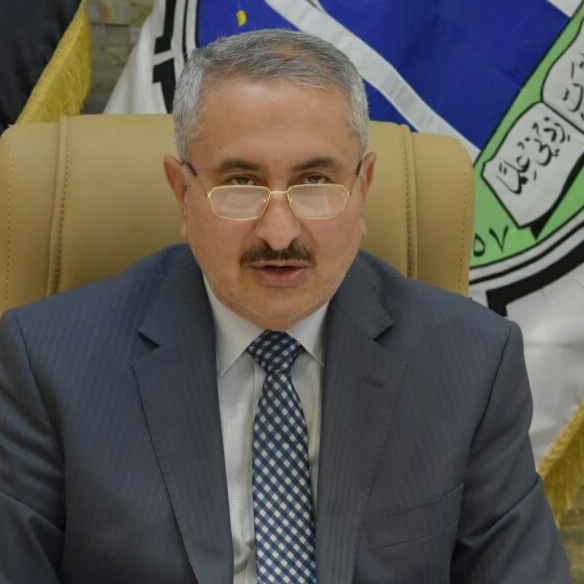
Ph.D. in Mechanical Engineering, University of Technology, Baghdad, 1998. Master of Mechanical Engineering, University of Technology, Baghdad, 1987. Bachelor of Mechanical Engineering, University of Technology, Baghdad, 1981-1982. Fellow of the British Institute of Management, (CMgr FCMI),2010.
Rector of the University of Baghdad: 2020 – Rector of of Al Ain University: June 2019 – 2020. Rector of the University of Kerbala: 1/4/2013 – 27/6/2019. Head Evaluator of Developing Dean Skills Program, the Association of Colleges (AoC). Scientific Assistant to the Head of the Technical Education Authority in Addition to the Duties of Dean of the Faculty, 2004-2005. Dean of the Technical College – Baghdad by-Election, 2003-2013. Assistant Dean at the Technical College – Baghdad, 2002-2003. Head of the Automotive Engineering Department at the Technical College – Baghdad, 2000-2002. Head of Machinery and Equipment Department at the Technical Institute – Suwayrah, 1998-1999. Official of the Scientific Unit of the Technical Institute – Suwayrah, 4-10/1/1994. Rapporteur of the Machinery and Equipment Department at the Technical Institute – Suwayrah, 1990-1994.
Member of the Iraqi Engineers Association. Member of the National Society for Engineering Inspection and Civil Protection, Baghdad. Fellow of the British Institute of Management.
Crude oil is one of the most important sources of energy in the world. To extract its multiple components, we need oil refineries. Refineries consist of multiple parts, including heat exchangers, furnaces, and others. It is known that one of the initial operations in the refineries is the process of gradually raising the temperature of crude oil to 370 degrees centigrade or higher. Hence, in this investigation the focus is on the furnaces and the corrosion in their tubes. The investigation was accomplished by reading the thickness of the tubes for the period from 2008 to 2020 with a test in every two year, had passed from their introduction into the work. Where the thickness of more than one point was measured on each tube in the sa
... Show MoreIn this study, aluminum alloyAA6061-T6 was joined by a hot press process with three types of material; polyamide PA 6.6 (nylon), 1% carbon nanotube/PA6.6 and 30% carbon fiber/PA6.6 composites. Three parameters were considered in the hot pressing; temperature (180, 200 and 220°C), pressure (2, 3, 4, 5 and 6 bar) and time of pressing (1, 2, 3, 4 and 5 minutes for 200ºC, and 0.25, 0.5, 0.75, 1 and 1.25 minutes for220ºC). Applied pressure has great effect on shear strength of the joint, corresponding to bonding time and temperature. Maximum shear strength was 8.89MPa obtained for PA6.6 at bonding conditions of 4 bar, 220ºC and 0.75 minute. For 30% carbon fiber/PA6,6 shear recorded was
The prostheses sockets use normally composite materials which means that their applications may be related with the human body. Therefore, it was very necessary to improve the mechanical properties of these materials. The prosthetic sockets are subjected to varying stresses in gait cycle scenario which may cause a fatigue damage. Therefore, it is necessary or this work to modify the fatigue behavior of the materials used for manufacturing the prostheses sockets. In this work, different Nano particle materials are used to modify the mechanical properties of the composite materials, and increase the fatigue strength. By using an experimental technique, the effect of using different volu
A new tool geometry was used to achieve friction stir spot welding (FSSW) in which the shoulder was designed separately from the rotating pin, and in order to examine weldment strength through the modified tool, a lap joints of AA2024 aluminum alloy plate 1 mm thick were welded successfully by using 6 mm pin diameter and varying process parameters (rotational speeds, tool nose geometry, and depth of tool penetration in the lower welded plate). Experimental tests indicate that the maximum average tensile shear load was 3100 N at the best selected condition. Microstructure examination and micro hardness test along the spot zones were investigated as well as measuring pin penetration load. Visual inspection of the welded spot surface shows a g
... Show MoreThree-dimensional nonlinear thermal numerical simulations are conducted for the friction stir welding (FSW) of AA 7020-T53. Three welding cases with tool (rotational and travel) speeds of 900rpm-40mm/min, 1400rpm-16mm/min and 1400rpm-40mm/in are analyzed. The objective is to study the variation of transient temperature in a friction stir welded plate of 5mm workpiece thickness. Based on the experimental records of transient temperature at several specific locations during the friction stir welding process for the AA 7020-T53, thermal numerical simulation is developed. The numerical results show that the temperature field in the FSW process is symmetrically distributed with respect to the welding line, increasing travel speed decreasing tran
... Show More